Dry
Packing
Dry
packing
is the process of putting
moisture-sensitive
plastic surface-mount devices in moisture-resistant bags or moisture
barrier bags (see Fig. 1) to prevent them from absorbing moisture
from the atmosphere. Moisture ingress into plastic packages can
result in popcorn cracking during board mounting. Popcorn cracking
refers to package cracking caused by abrupt vaporization of internal
package moisture.
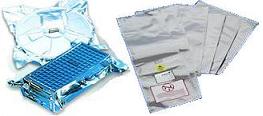
Fig.
1. Examples of moisture barrier bags
Different
packages have different
levels of moisture
sensitivity. The amount of time that the units can spend
outside the moisture barrier bag once it is opened is known as the
floor life. Thus, units must be board mounted before the specified
floor life is reached. Units can not stay indefinitely inside the
moisture barrier bag too.
Shelf
life
is the amount of time that the units can be kept inside the bag from
the date the bag was sealed. The shelf and floor lives of a lot
must be labeled on the dry pack of the lot.
Prior to
dry packing, units must be
baked
to
drive any internal moisture away.
JEDEC
J-STD-033 gives the recommended bake conditions and durations
prior to dry packing.
The baked
units, which should be in tubes, trays, or a reel, are then put
inside the moisture barrier bag along with, if possible, a
desiccant
(see Fig.
2) for moisture absorption and a
moisture
indicator card
(see Fig. 3) which can indicate the highest moisture level that the
units have been exposed to inside the bag. Dry packing is completed
by
vacuum-sealing
the bag.
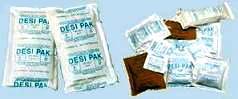
Fig.
2. Examples of desiccant bags
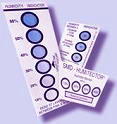
Fig.
3. Examples of humidity indicator cards